We are delighted to introduce KV SMART SYSTEMS, a company founded and led by technically qualified women entrepreneurs with over 8 years of experience in the fields of Industrial Automation, Instrumentation, and Design.
Read More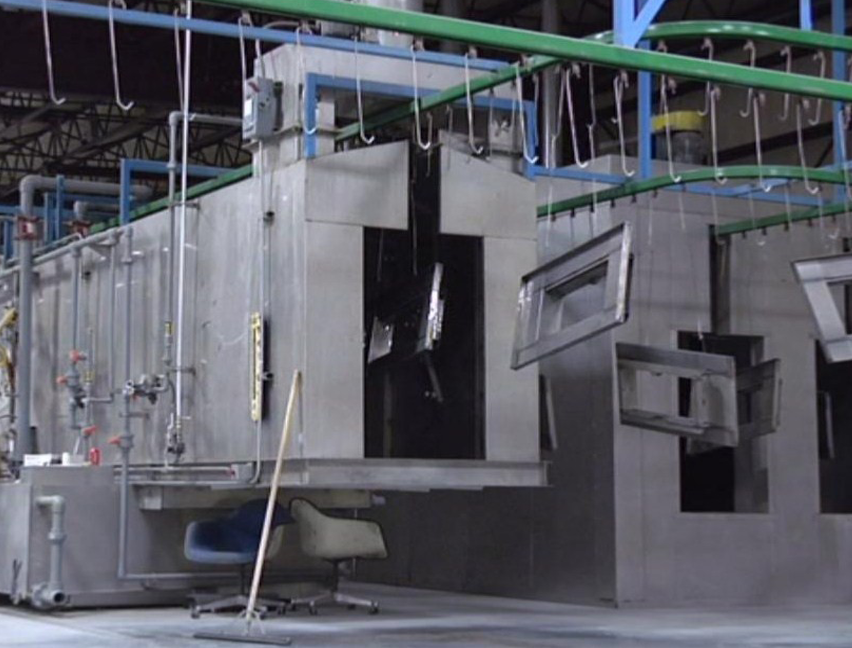
AUTOMATING A POWDER COATING SYSTEM CAN SIGNIFICANTLY ENHANCE EFFICIENCY
Automating a powder coating system can significantly enhance efficiency, consistency, and throughput in industrial applications.
Below is an overview of the components and equipment involved in an automated powder coating system, along with their respective roles:
1.Automated Powder Coating Booth.
Enclosed Booth: Designed to contain the powder and minimize contamination.
Recovery System: Automated systems for collecting and recycling overspray powder, typically using cyclones or cartridge filters.
- Automatic Powder Spray Guns: Multiple electrostatic spray guns mounted on reciprocators or robots for precise and uniform application.
- Reciprocators and Robots: Automated arms or reciprocators move the spray guns to ensure consistent coverage and reduce manual labor.
- Control Units: Centralized control units manage the operation of spray guns, adjusting parameters like voltage, air pressure, and powder flow.
2.Automated Application Equipment.
- Conveyorized Ovens: Continuous curing ovens where parts move through on a conveyor system, allowing for high-volume processing.
- Temperature Control Systems: Automated temperature control to ensure optimal curing conditions and energy efficiency.
3.Automated Curing Ovens.
- Automated Hoppers: Systems that automatically refill powder from bulk containers to spray hoppers, maintaining a consistent supply.
- Fluidized Beds: Automated systems ensure the powder is aerated and ready for smooth application
4.Powder Feed System.
- Automated Washing Stations: Multi-stage washing systems with automated control for degreasing, rinsing, and applying conversion coatings.
- Dry-off Ovens: Automated dry-off ovens to remove moisture from parts before coating.
5.Pretreatment System.
- Overhead Conveyors: Automated conveyor systems transport parts through pretreatment, coating, and curing stages.
- Automated Racking Systems: Racks designed to hold parts securely and ensure proper grounding during the coating process.
6.Conveyors and Material Handling.
- Automated Supply Management: Systems to monitor and replenish powder supply automatically, reducing downtimes.
7.Powder Coating Powders.
- Ventilation and Filtration Systems: Automated systems maintain air quality, capture powder particles, and ensure proper airflow within the facility.
8.Environmental Control Systems.
- In-line Thickness Gauges: Automated measurement of coating thickness to ensure consistency and quality.
- Cure Testers: Automated systems to verify that coatings have properly cured and adhered to the substrate.
9.Quality Control Equipment.
- Protective Enclosures: Automated safety features to protect operators and maintain a safe working environment.
- Fire Suppression Systems: Automated systems to detect and suppress fires in the booth and curing oven.
10.Safety Systems.
- SCADA Systems: Supervisory Control and Data Acquisition systems monitor and control the entire powder coating process.
- Data Logging and Reporting: Automated logging of process parameters and production data for quality control and traceability.
11.Monitoring and Reporting.
- 1.Consistency and Quality: Automation ensures uniform application and curing, resulting in consistent high-quality finishes.
- 2.Efficiency and Throughput: Automated systems can operate continuously, increasing production rates and reducing downtime.
- 3.Reduced Labor Costs: Automation reduces the need for manual labor, lowering labor costs and minimizing human error.
- 4.Material Savings: Efficient recovery and reuse of overspray powder reduce material wastage.
- 5.Enhanced Safety: Automated systems reduce operator exposure to powder and chemicals, enhancing workplace safety.
- 6.Energy Efficiency: Optimized control of curing ovens and other systems can lead to significant energy savings.
Benefits of Automation in Powder Coating.
Example of an Automated Powder Coating Process.
- 1.Pretreatment Stage: Parts enter the automated washing station, where they are cleaned and prepped.
- 2.Dry-off Stage: Parts move through the dry-off oven to remove any moisture.
- 3.Coating Stage: Parts enter the powder coating booth, where automated spray guns apply the powder.
- 4.Curing Stage: Coated parts move through the conveyorized curing oven.
- 5.Quality Control Stage: Parts are inspected using automated thickness gauges and cure testers.
- 6.Finished Products: Parts exit the system, ready for packaging and shipment.
Implementing automation in a powder coating system can significantly enhance productivity, quality, and overall operational efficiency, making it an attractive option for industries looking to optimize their finishing processes.
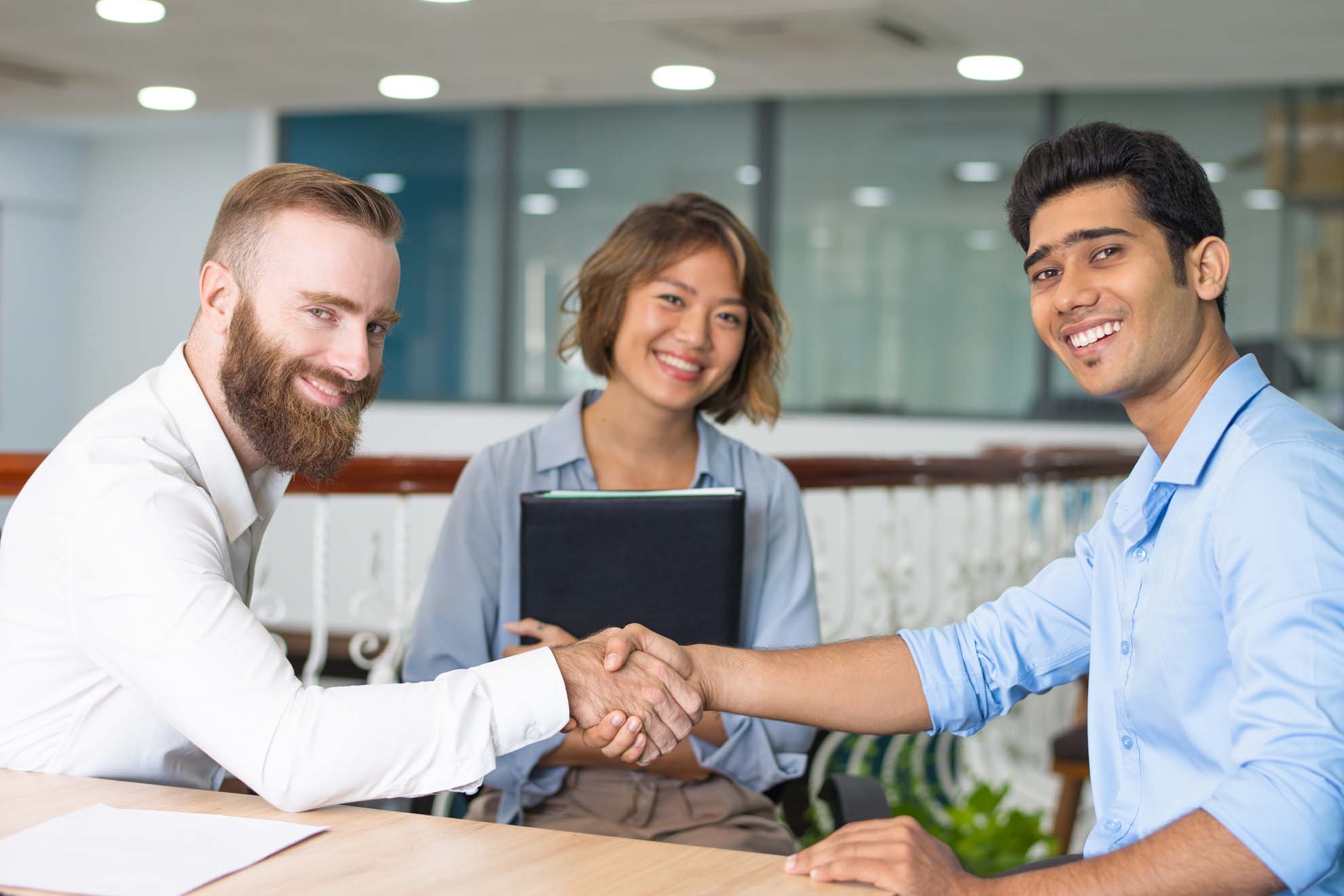
Why Creote
Affordable & Flexible
Must explain too you how all this mistaken idea of denouncing pleasures praising pain was born and we will give you complete account of the system the actual teachings of the great explorer.
- Cost-Effective Services
- Helps Reduce Business Risks
- Management of Employee Performance
- Increasing Company’s Agility
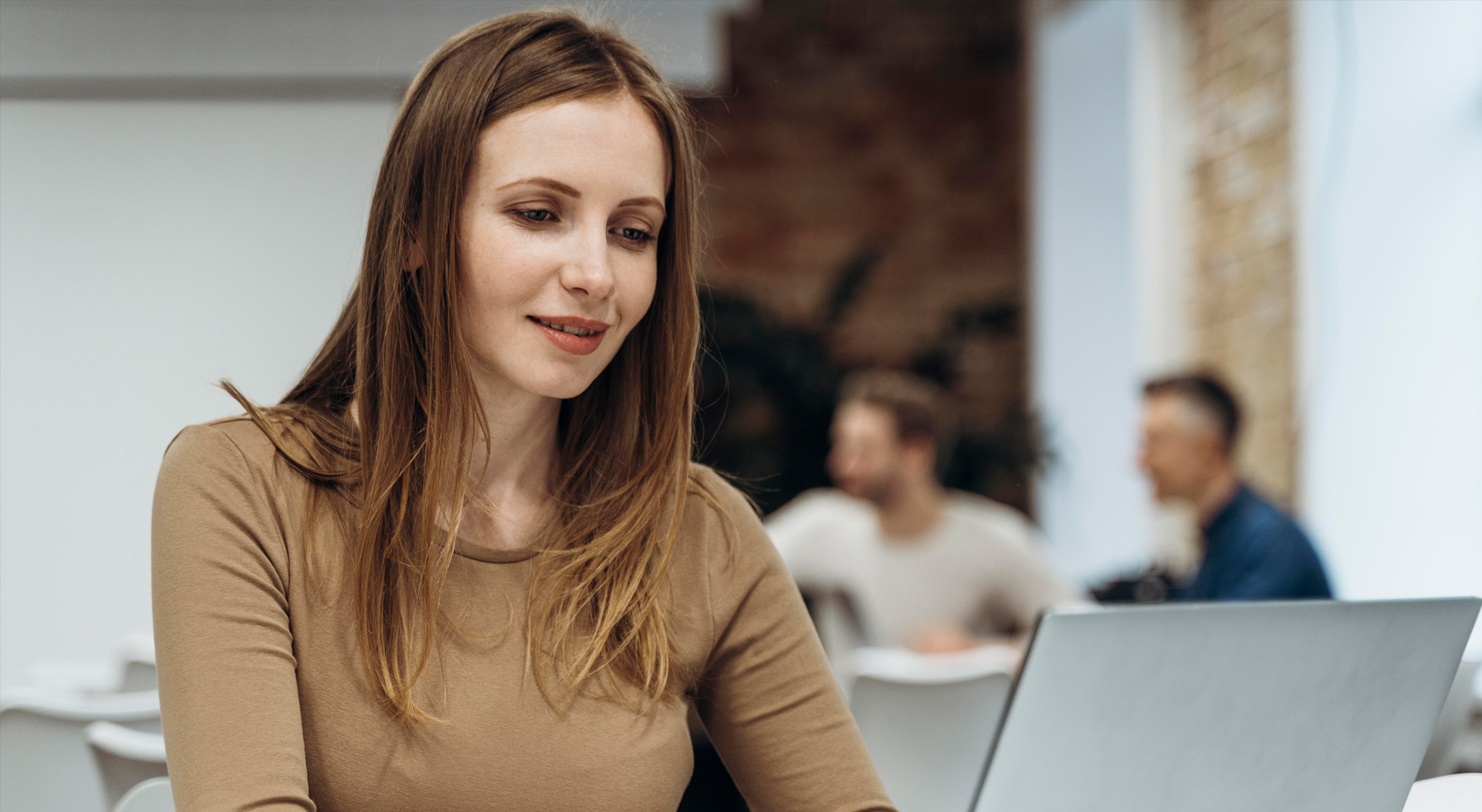
Why Creote
Affordable & Flexible
Must explain too you how all this mistaken idea of denouncing pleasures praising pain was born and we will give you complete account of the system the actual teachings of the great explorer.
- Cost-Effective Services
- Helps Reduce Business Risks
- Management of Employee Performance
- Increasing Company’s Agility